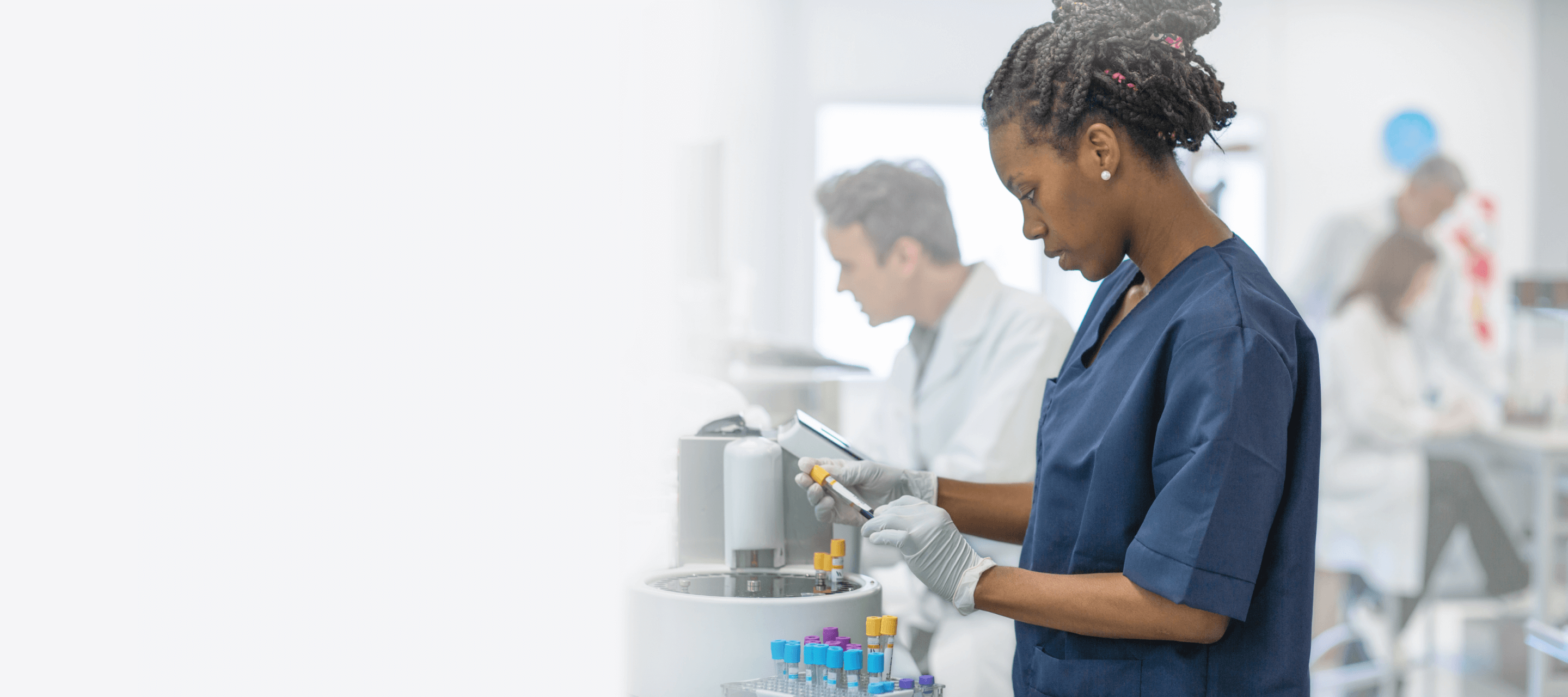
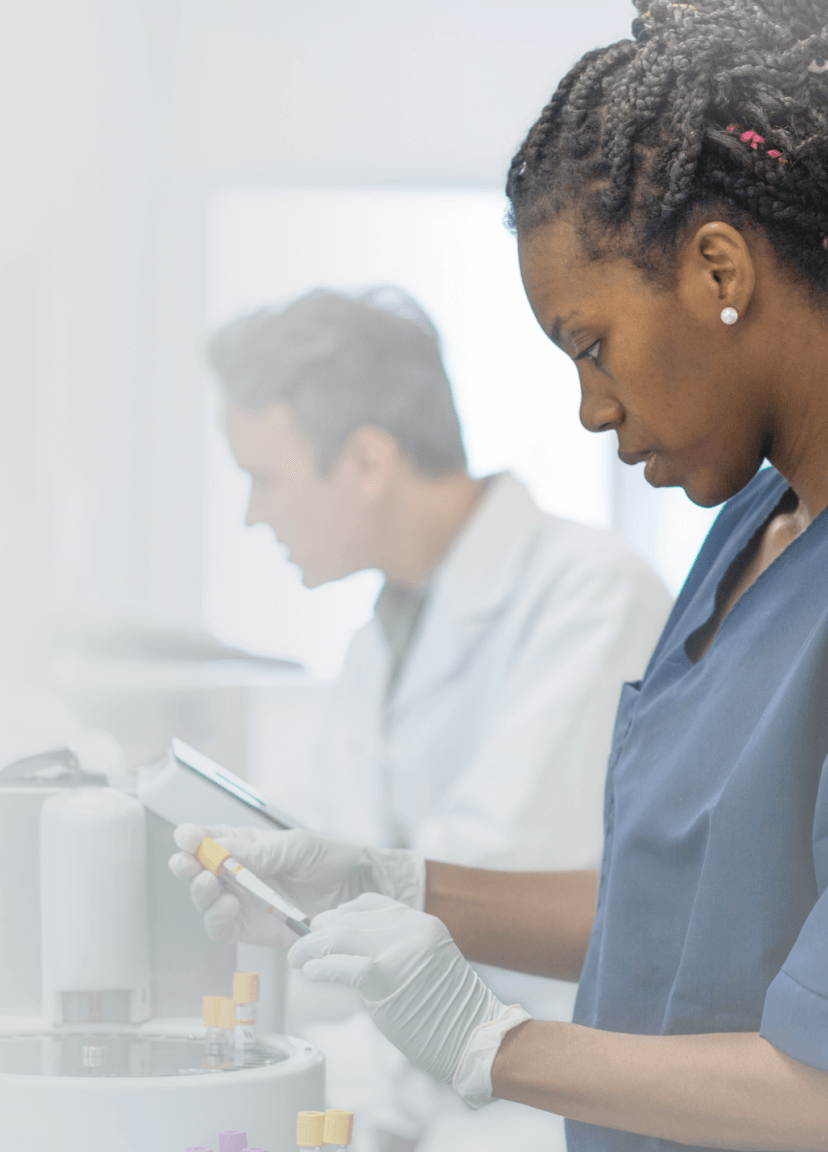
NHS partners with Automata to automate testing facility
Overview
In 2021, in the height of the COVID-19 pandemic, Automata worked with the University Hospital Southampton (UHS) NHS Foundation Trust to automate Reverse Transcript Loop-mediated isothermal amplification (RT-LAMP) testing.
The RT-LAMP community testing rollout
In June 2020, a pilot programme for weekly coronavirus (COVID-19) testing began, using a ‘no-swab’ saliva test. Saliva is tested for COVID-19 using RT-LAMP-based detection procedure.
The decision to utilise this process was driven by the advantages it has when compared to the more widely used Polymerase Chain Reaction (RT-PCR) method. RT-LAMP tests can be turned around more rapidly, and the process also has no swab constraints. Additionally, RT-LAMP has a higher sensitivity and specificity than antigen lateral flow devices.
The UHS subsequently set up a new programme using non-invasive saliva collection to deliver COVID-19 test results to participating schools, colleges, universities and other participating settings within 24-48 hours.
The demands of testing at scale
The UHS was tasked with delivering a testing programme to cover the local population of Hampshire and the Isle of Wight. In order to enable testing for a wider section of the community, significant expansion in testing capacity and a substantial increase in the number of daily processed tests was required.
The UHS required an automation solution for aliquoting saliva, and an automation partner that could work flexibly and deliver rapidly. This was critical, as it was during a time when national institutions were competing to expand testing and recruiting from an already stretched diagnostic workforce pool. Indeed, nationally, The Institute of Biomedical Science estimates that in 2021, the demand for testing in UK molecular microbiology labs has jumped from around 300,000 a year, to 300,000 every single day.
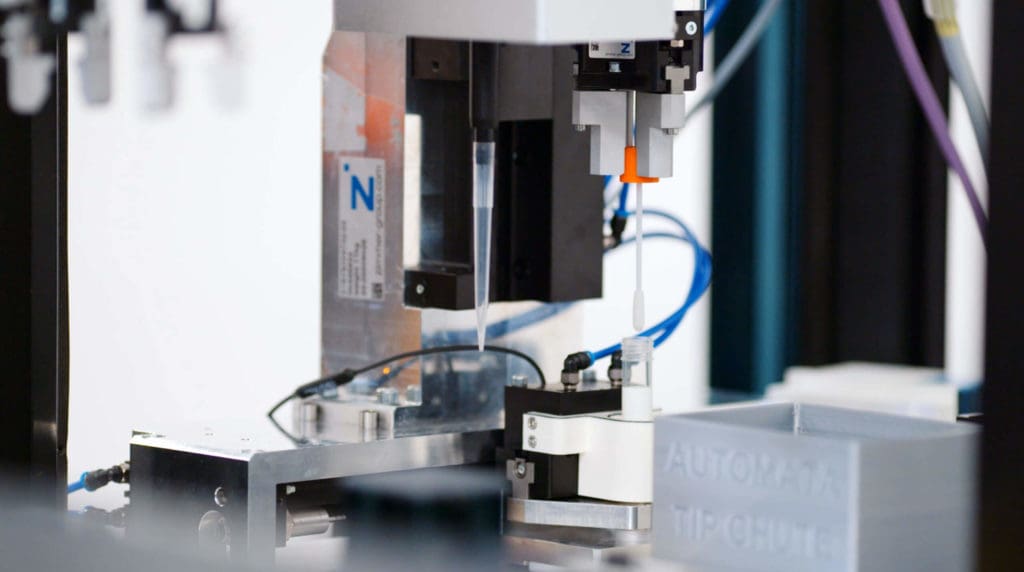
The Solution and Automata’s Involvement
Automata was initially working with the UHS as a robotic supplier, but as the programme continued, their relationship grew into a partnership. The versatility of Automata Labs, and its technology, allowed Automata to design bespoke solutions, with systems reprogrammed live on-site to meet changing requirements.
Working alongside engineers from the programme, Automata developed a proof of concept, demonstrating and testing it before moving to full production. The design, testing, manufacture and installation of automated liquid handling systems took six months end-to-end, including production and design time. Due to the flexibility of Automata’s automation approach, the design was able to evolve with the UHS’ changing needs while still in production.
Modular automation stations:
Automata’s LAMP solution combines multiple modular units to automate the majority of the sample aliquoting process, utilising a conveyor belt to form an end-to-end testing system. Each unit houses a robotic arm, seamlessly fitting together to process the saliva sample for testing, liquid handling, auto sampling, thermocycling, reformatting and reading part of the testing process
Service team:
Automata deployed a service team ‘on site’ in Southampton, meaning that a trusted engineer could be deployed within 15 minutes if required
The results have been transformative. Automation has supported the UHS in processing unprecedented volumes of tests per day for the existing facility, reducing the role of human error. It has also made lab practices safer for staff compared to previous solutions and removed humans from potential exposure to biohazardous substances during the process, protecting them from infection.
Increased scale: Automata has supported the programme in rapidly scaling up capacity to meet its new high throughput targets, allowing for a greater number of participants to be tested and reducing chains of transmission
Traceability: The enhanced traceability has allowed UHS to streamline their data gathering and ensure samples are processed in a timely and repeatable manner
Reduced errors: The adoption of integrated barcode scanning for each vial in and out of the automation system has eliminated the potential for manual tracking errors ensuring robust repeatable result, clinical quality validated by a national test and trace facility
Staff utilisation: The introduction of an automation system has supported UHS with workforce planning and reduced pressures on short-term recruitment, while reducing the risk that core deliverables are impacted by staff absences (due to illness)
The success of the partnership has led Automata and UHS to explore further opportunities for how Automata can automate other manual elements of the existing RT-LAMP testing process, and partner further with UHS to streamline other complementary diagnostic processes.
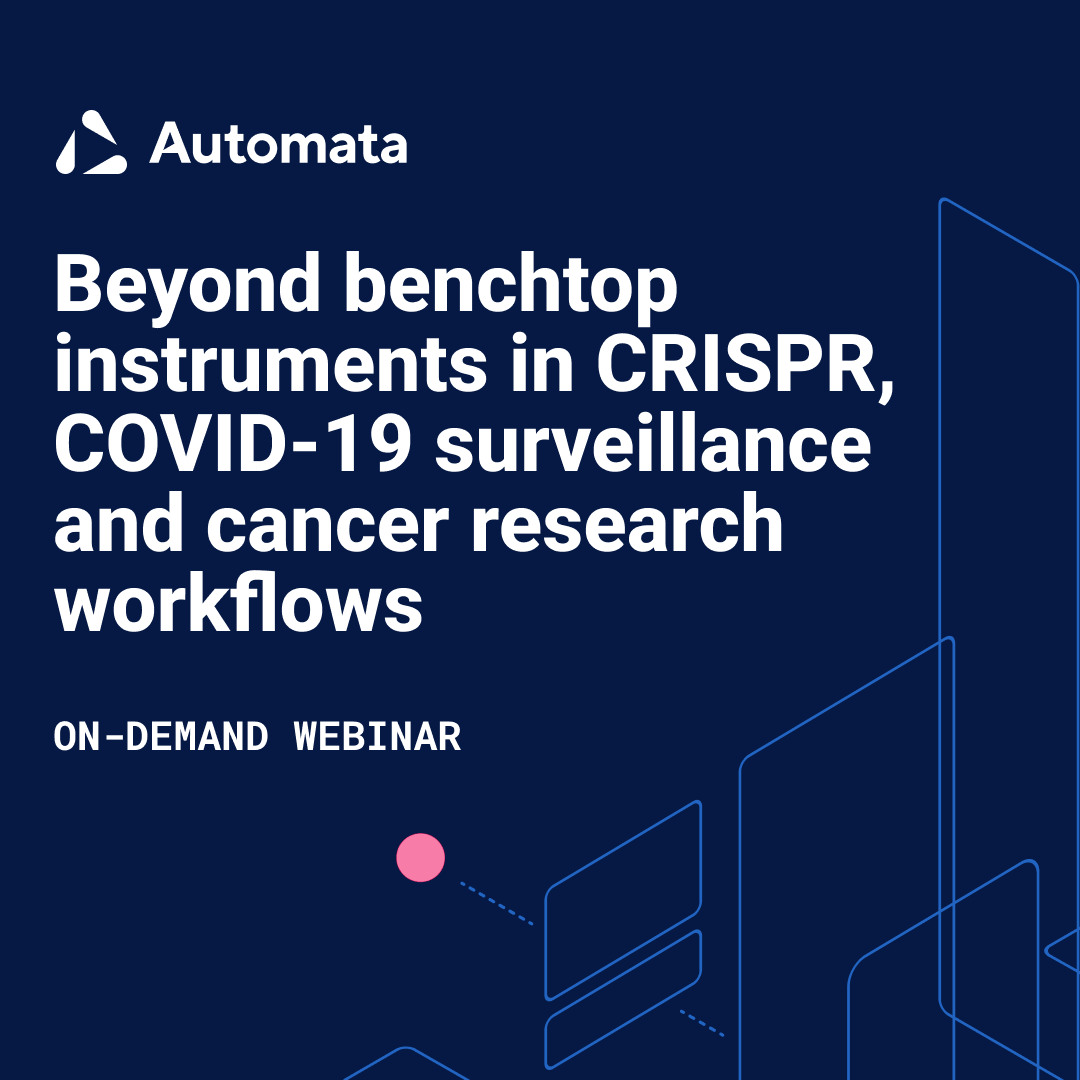
Thinking beyond the benchtop instruments
Explore how automation is transforming key genomics workflows, from CRISPR to COVID-19 and cancer research