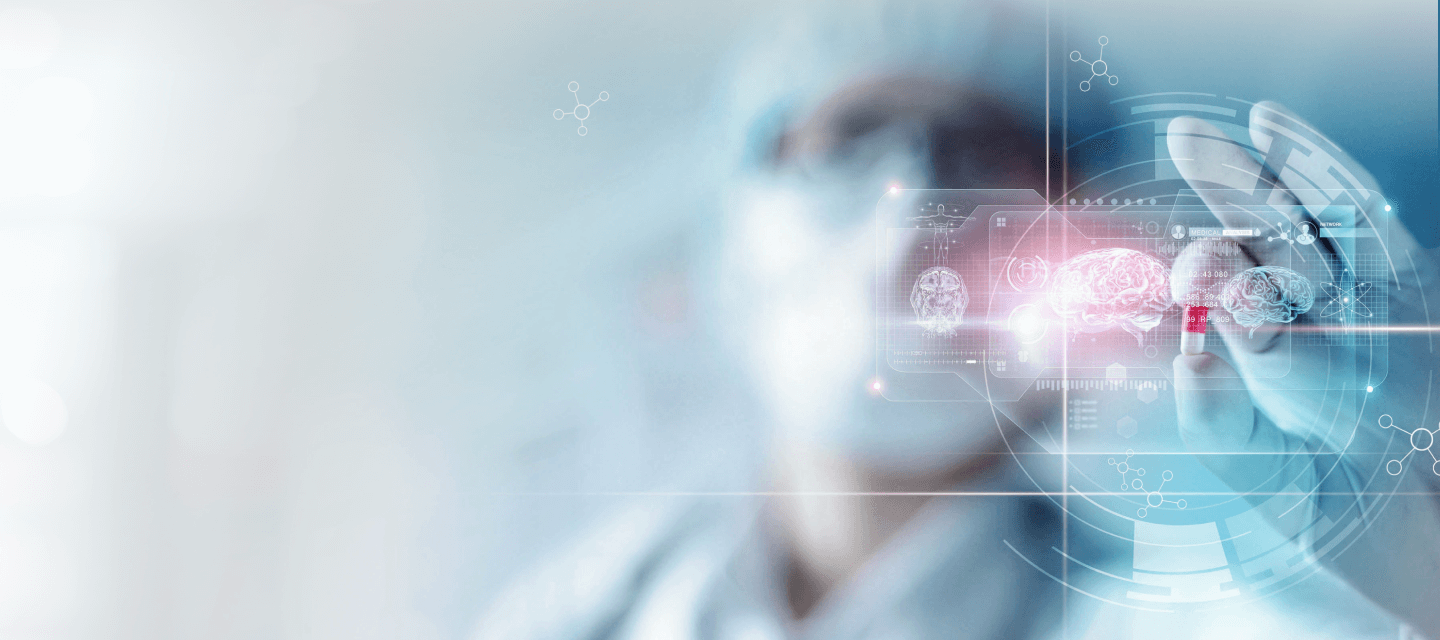
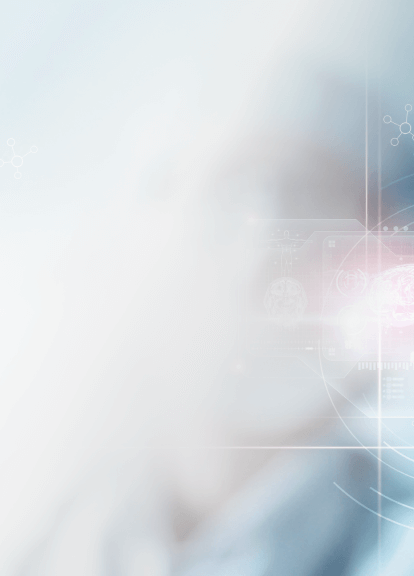
What is lab 4.0 & digital transformation in the lab?
We are currently in the midst of a fourth industrial revolution. Titled “Industry 4.0”, this refers to the development of technology for manufacturing to move towards a digitalised and connected industry. The first three industrial revolutions involved the mechanisation of production using specific technology:
- Steam (1765)
- Electricity, gas and oil (1870)
- Electronics, telecommunications and computers (1969)
The fourth industrial revolution aggregates technology using automation and robotics to connect automated processes and equipment. This allows for traditionally manual processes to be monitored and controlled by tailored technology.
Industry 4.0 is being applied to science around the world, modernising the laboratory environment to keep up with the pressures of innovating laboratory methods.
What is lab 4.0?
Lab 4.0 refers to a branch of Industry 4.0 that encompasses the move towards intelligent technology, adopting digitalisation and automated technology to enhance laboratory processes. Optimising workflows to boost efficiency and productivity allows laboratories to meet the growing demand for increased output capacities. Automation provides reliable, reproducible, scalable, cost- and time-efficient results with the ability to meet capacity requirements.
Leveraging a lab-digital transformation through automation, robotics, and artificial intelligence will revolutionise the standard laboratory working day. Future predictions anticipate that laboratories will substantially invest in their technology to be entirely hands off. Automation is not a new concept, however the increase in its accessibility, flexibility and adaptability offers the opportunity to streamline workflows, boosting productivity and efficiency.
Benefits of lab 4.0
The benefits of digital transformation of laboratories are endless:
- Boosting productivity: Automation can improve the efficiency and volume of lab workflow turnover by 30-40% (1). Standardisation of processes can provide faster manufacturing and research outputs. Furthermore this has a positive impact downstream on cost reductions, enhanced reliability, and reproducibility, thus contributing to overall company productivity.
- Cost reduction: It is estimated that automation brings with it a 20% reduction in costs when integrated with established processes (2). Switching from laboratory processes that require expensive manual labour to automation maintains reliability and efficiency but reduces the costs of long working hours and highly skilled staff. Investments in automation can be expensive, however evidence has shown that investing in Lab 4.0 can lead to long-term profit.
- Employee satisfaction: Removing repetitive tasks and replacing manual labour with computational solutions increases staff satisfaction. Allowing highly skilled individuals to work on other meaningful tasks and research innovation increases the capacity of R&D within companies.
- Lights out labs: End-to-end automation workflows can be fully operational 24 hours a day, enhancing the productivity and capacity of manufacturing and research processes. Automated processing and analysis of data in real-time boosts productivity, with efficient integrated quality control measures increasing delivery reliability by 14% (2).
Embracing the lab 4.0 revolution with lab automation
Embracing automation can begin with small steps, such as implementing changes into parts of manufacturing and research processes like automated temperature-controlled incubators or DNA extraction machinery. At the other end of the scale, fully automated systems can overhaul complex workflows from sample handling to data analysis. Digitalised laboratories are becoming the new norm, with the generation of more complex data such as -omics data. Providing end-to-end automated operations can help labs scale and standardise workflows to meet the growing demand for genomics testing.
Investing in Lab 4.0 technology can enhance connectivity and support collaboration amongst laboratories worldwide. Companies can streamline production, analysis and quality control auditing to a central hub, maximising the efficiency of data exchange and potential for company innovation. Automated lab benches are the latest trend to transform laboratory ecosystems. Automation offers the opportunity to revolutionise current working processes across the public and private sectors. The facilitation of faster delivery of diagnostic results and shortening of drug development times ultimately leads to better patient care.
References:
- Yan Han et al., “Digitization, Automation, and Online Testing: The Future of Pharma Quality Control,” McKinsey & Company (McKinsey & Company, January 4, 2019), https://www.mckinsey.com/industries/life-sciences/our-insights/digitization-automation-and-online-testing-the-future-of-pharma-quality-control.
- Kamal R, “What Is Pharma 4.0?: Use Cases, Trends & Benefits,” What Is Pharma 4.0?: Use Cases, Trends & Benefits, July 21, 2022, https://www.intuz.com/blog/what-is-pharma-4.0-use-cases-trends-and-benefits.
- “Fully-Automated Genomics Workflows,” Automata, https://automata.tech/applications/genomics/.